![]() | ![]() |
---|
ABOUT WIND UP TOY
ABOUT
We are Rafael, Matthew, Pilar and Isabel, four mechanical engineering students from UIUC. We were asked to reimagine a specific product, focusing on design for manufacturability. We chose a Wind Up Toy from Kikkerland, a small company which is very design oriented. In order to find out as much as possible about our toy, we disassembled it and analyzed every piece and material. We conducted cost analysis, as well as several manufacturing quality tests. We took measurements, created sketches, and brainstormed until we came up with the best idea for an improved product. Finally, we recreated the product using 3D CAD software and 3d printed the most important pieces. All our results and milestones will be posted in this website for everyone to see.

DESIGN REQUIREMENTS AND RESOLUTION
COST OF PRODUCTION
We feel that Cost of Production is the first and foremost element a company should consider for their products, since it will determine both their profit and market revenue. In order to achieve the lowest cost of production possible, we worked to reduce the number of pieces since fewer pieces generally corresponds to lower production costs.
LIFE EXPECTANCY
Life expectancy is also key to making a large profit. Most companies aim for a high Life Expectancy to boost customer satisfaction, since the brand’s image depends on the quality on their products and the public’s opinion. We designed the new parts taking into account specific characteristics that make them very resistant so that the toy will endure.
CONTACT FRICTION
A great contact friction coefficient means that the toy will virtually never slip or lose its balance. It also translates to a longer product life, since the product is less likely to fall. We selected materials which show these qualities.
BILL OF MATERIALS
PRODUCT TREE ANALYSIS
After we found out what our objectives were for the project and viewed the disassembled parts, we created a product tree to decide what changes could be made to improve the product. In the center was the main issue with the product, the red inner circles were specific issues with the product, the green inner circles were solutions to the specific issues with the product, and the outermost boxes were further descriptions explaining the issues (red) or the benefits (green). Creating this tree broke down exactly how we could improve the existing problematic parts of the toy. We then decided which specific parts we actually sought to improve.

COMPANY MARKET SHARE AND PRODUCT SALES ANALYSIS

After performing the product tree analysis, we analysed the potential for improvement of our product, by investigating market and sales data. We found that “Kikkerland Design” has been operating since 1992, and currently has an annual revenue of 1.2 million USD. The average selling price of their products is 33 USD. Assuming that their profit margin is ⅔ the cost of their products, they sell about 36,400 products a year (1.2 million divided by 33). The company is mostly internet based, and employs under one hundred people. Kikkerland does not have any big competitors. Rather, its biggest competition is the collection of smaller companies that make cheaper/more affordable wind-up toys that can be bought in quarter machines or in large quantity at places like walmart or party city.
To deduct market share, we used a series of assumptions based on real market facts. First, the entire world toy market is worth 88.8 billion USD, according to the “statista” website. We then assumed that the wind-up toy market was about 0.02% of the entire toy market. In other words, 2 out of every 10000 toys bought in stores will be wind-up toys. Using these figures, the total wind-up toy market is approximately 17.76 million USD. Since Kikkerland has an annual revenue of 1.2 million USD, they hold 6.76% of the wind-up toy market, or 0.00135% of the entire toy market.
SERVICE

We have estimated that the cost to manufacture this toy is about $10.00. We used the rule of thumb that the manufacturing cost is approximately ⅓ the cost of the price.
In our opinion, the best manufacturing choices made for this products are related to the material selection. The materials used for all parts of this toy, as far as we can tell, are steel, silicone, and nylon. Due to the wear resistance and good sliding properties of nylon, this material is the best choice for gears. Nylon is relatively easy to CNC machine to close tolerance requirements, which makes for very accurate parts that can be quickly produced. Also it is fairly inexpensive itself. Steel also has good properties such as oxide resistance and light weight, which make for a lighter and more lasting product.
Another good decision, is the usage of standard issue pieces for the shafts. This reduces the design workload, as well as the production cost. Furthermore, these standard shafts are very cheap to buy from suppliers.
Finally, there are some really good aspects of the main body design. Both body parts are joined by a slot system instead of a screw system. This significantly reduces the cost, since the assembly of the small screws would be costly and time consuming. Also, this reduces the potential hazard for any children in contact with the toy. The body itself was easy to manufacture since it uses simple metal bending and hole punching.
Then, we completed a QFD matrix, or quality function deployment matrix. It allowed us to select certain design and customer requirements, and to rate their significance. It is also a very good way to identify correlations between product characteristics.

After completing the QFD matrix, we have identified several focus points for product improvement. Two of the design requirements, which are cost of production and material quality stand out because they have many correlations with the other requirements. This means that any changes to those factors will have a significant effect on the overall product characteristics. Simply put, we believe that increasing material quality and decreasing cost of production, while not easy to do, will lead to a bigger market share.
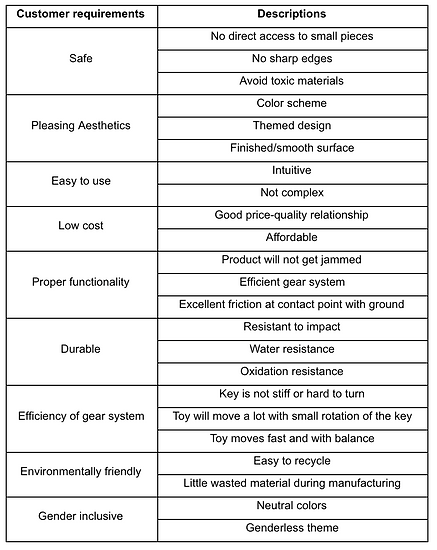
Here is the list of costumer requirements used for the QDF matrix, with more details.
Product improvement based on QFD results:
LEG MECHANISM IMPROVEMENT
We intend to improve producibility by designing a simple component to substitute the current leg mechanism. This simple component will consist of only one solid part made with injection molding which should be easy to manufacture/fabricate. Currently, each leg sub-assembly contains 7 different components which definitely leads to unnecessarily long assembly times. Improving the design of the legs for our toy will surely translate into a higher production rate, as well as simplifying design, outsourcing, assembly, and production.


MAIN BODY IMPROVEMENT
A protective case will be created and added to every product to improve aesthetics and to increase product life expectancy. This case will be transparent in some locations to allow customers to see the gears in motion (a really cool feature of our product), and will have a specific theme for other locations.

CAD MODELING
Our toy is a very complicated product from an assembly point of view, with many components which intersect with each other through different methods and contact angles. In the CAD, we chose to ignore the inner mechanism of the toy since we will not be modifying it in any way. We instead chose to focus our effort in the legs and overall body geometry, which are the main components we will be modifying.
Before developing a CAD model for our improved parts, we designed the main components of our current product in Creo. The following images are assembly views of all of the CAD modeled components.
Captures of our CAD model:

"APRIORI" COST ANALYSIS
Using the CAD model, an aPriori analysis was performed to estimate the overall cost of each part currently used in the toy, as well as the cost to assemble each individual leg. The aPriori analysis was performed for a production volume of 36,400 products sold per year and a production range of 10 years.
For purchased parts, such as the shafts, we estimated the cost using online catalogs since these components are generally purchased from large suppliers. The cost of purchasing each shaft came out to be approximately 0.007 USD.
"APRIORI" RESULTS
When running the assembly model through aPriori, we basically only had half of our entire assembly created so the results we obtained were multiplied by two to ensure correct analysis results.
The values in the “Totals” row were calculated using the equations below:
Material Cost: Total= sum(Material Cost * quantity)
Piece Part Cost: Total= sum(Piece Part Cost * quantity)
Fully Burdened Cost : Total= sum(Fully Burdened Cost * quantity)
Total Capital Investments: Total= sum(Total Capital Investments)
When determining the overall cost per part, we decided to use the fully burdened cost and add it to the total capital investment cost divided by the number of parts that will be made using each machine (a total of 364,000 parts). Thus, our final total cost per part is 34.654 USD. This value is extremely high considering that we are only determining the cost of the components which we are improving, which only corresponds to approximately 1/3 of the production cost for the entire product. However, these values are valuable for comparison with the aPriori results obtained for our redesigned components since both aPriori simulations should yield values which are greater than expected. Generally, the ratio between the estimated cost values should still provide high quality insight into the improvements made.
Analysis was performed to determine possible reasons why the aPriori results were unreasonably high. The conclusions are as follows:
The cost would go down if we were to produce our parts in a more industry based country with cheaper human labor, such as China. According to aPriori, the costs would go down by 2/3 (66.67%) when switching from US to China specifically.
Furthermore, Kikkerland does not manufacture each of there pieces since they are a relatively small company. Buying certain components from third parties would reduce total cost, especially when it comes to standardized components such as gears or shafts. These are very present in our product, which means the price variation would be significant. Additionally, even the customized parts are probably not manufactured by Kikkerland but rather ordered to be manufactured by a supplier that is specialized on that specific kind of manufacturing.
Lastly, the manufacturing process we selected might not have been the most optimal and there is probably room for improvement in that area. However, it is extremely difficult to determine the exact manufacturing process and material used by the company (if it was easy, then it would be easy to replicate their product). Thus, it is safe to assume that they have optimized their manufacturing techniques and process to be the most cost effective. This is another reason why our cost estimate is higher than the actual cost.
Final Bill of Materials Spreadsheet Table with aPriori Results

OUR DESIGN SKETCHES:
PUGH MATRIX
Here is our completed Pugh matrix:

After analyzing the Pugh matrix results and aPriori’s estimated production cost, we reached the conclusion that fusing the leg mechanism into one solid piece is the most effective measure we can possibly take. It allows us to decrease our expenses, by manufacturing only one geometrically complicated piece per leg, rather than 5 components. This is reflected in the new cad, which shows a possible implementation of this concept. All the legs have been fused around a disk shaped piece. This solid joint replaces the former very expensive articulation.
We also decided to remove the silicone socks from our legs. Instead, we designed the feet with an ample contact surface, which we hope will provide enough support. The rectangular feet are also slightly curved on the edges, to ensure smooth transitions when the toy is walking.
The new solid joint will then be attached to the main body through a straight shaft. This standardized part is inexpensive, especially when compared to the former asymmetrical curved shaft.
Lastly, we changed the main body of our toy. In the previous cad model the body was left as a rectangular box, to represent the gear and coil mechanism. While we will not be modifying these pieces in any way, we have decided to cover them with a clear case. We intend to ensure kids safety when interacting with our toy, while still exposing the inner pieces and maintaining the educational features. Additionally, the case is meant to improve durability, as well as the toy’s balance, by increasing its symmetry and inertia.
Below are pictures of the final CAD modeling.

EXPERIMENT WITH PROTOTYPE
We did an experiment in order to determine the width of both the upper and lower leg that would provide the leg mechanism with the highest resistance to failure under working conditions. These were the values fixed for design and performance variables:

After incrementing the weight placed on the legs until they either snapped or bent for the four possible combinations, we obtained the following results:
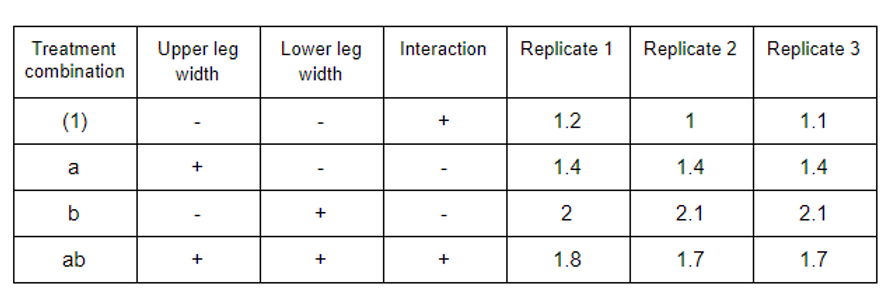
According to the results, the best scenario is the one in which the upper leg width is set to low while the lower leg width is high. This is to be expected since the torque applied to the lower part of the leg is higher, torque being force times radius.

FINAL APRIORI RESULTS
Our final aPriori results show that the product cost is significantly decreased after our design improvements. This is mostly due to the lower number of parts involved in the manufacturing process. In addition, the material we used (plastic) was much cheaper than the materials used in the original product (metal and silicone). It should be noted that adding the case may have added a slight cost increase, however we believe it would be low when compared to the benefits. If the cost were not low, the case could be removed and not manufactured. We are very happy with the result, we believe it is a much more efficient product and that it will allow the manufacturing/selling company to increase their revenue.

FINAL CONCLUSIONS
To conclude this design project, we must analyze the overall improvements of our new toy design by comparing it to the original component that is available for purchase on Amazon. The main comparisons revolve around the concepts of cost, function, quality, environmental effects, durability, and manufacturing and assembly times.
We made a brand new casing to put around the product. There was no casing in the original product and all the sensitive gears and innards of the product were exposed. Creating the case protects these exposed components and adds durability to the product as a whole. It also adds a bit more functionality to the product as well. Since the product is more durable, the product can handle more abuse, meaning children can play with it as they desire. This freedom is what adds more functionality. The cost of the product as a whole slightly increases when the case is added but the cost increase is minimal compared to the amount of durability and functionality that comes with adding it.
It is also valuable to briefly touch on environmental effects; our plastic is recyclable which minimizes the harmful effects to the environment. Also, our part helps reduce the harmful effects the original may have on the environment. The original product uses metal and silicone legs and socks. The production of these individual pieces can cause harmful effects to the environment whereas our recyclable plastic legs minimize this harm.
Additionally, we also decided to make the legs and joint one piece and make them out of plastic. The original product had each leg and the joint as separate components (8 total parts for each “rotating leg” piece) that would need to be assembled individually, a total of six times. Making the leg and joint one piece reduces the assembly time and the amount of assembly required.
Furthermore, focusing on functionality, our new and improved legs are better than the original because there is no chance that the legs could come undone or fall off from the joint. Since it is one piece it is physically impossible for it to “fall out” from the joint. With that in mind, the durability of the new product takes a slight "hit" when making the joint and legs a single piece and out of plastic. In order for the leg to be separated from the joint it would have to break off, which can be viewed as a plus. However, plastic is less durable than metal, which makes the chance of the toy breaking slightly higher. When comparing that to the cost saved by doing this, it is a "hit" that is worth taking. Also, since there is not sub-assembly time and the material is cheaper, the cost goes down a fair amount when producing the product. Since the legs are a large part of this product, decreasing the cost of these greatly influences the cost of the product as a whole.
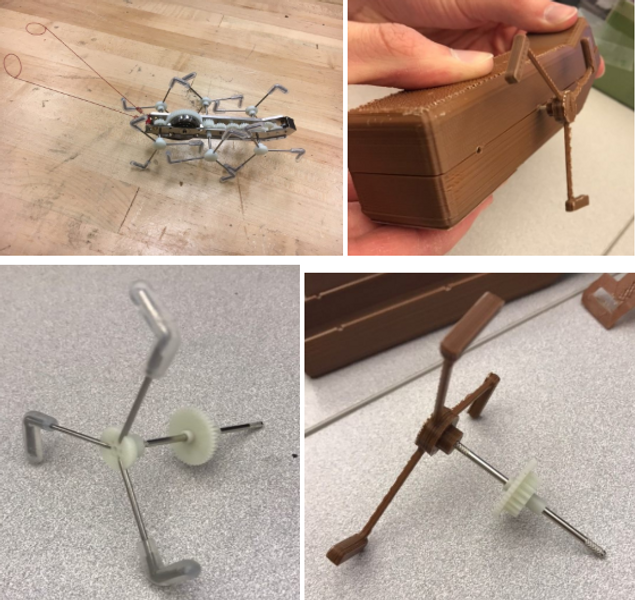